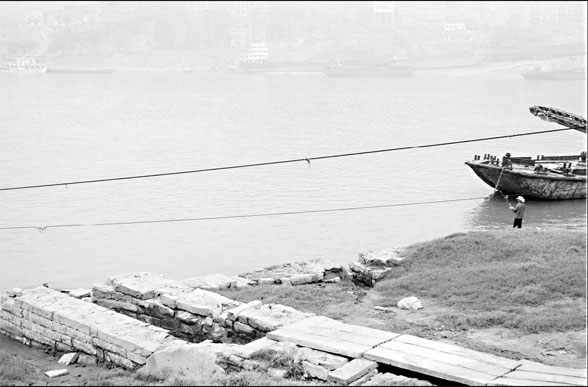
A Fuling resident fishes in the once heavily polluted Wujiang River, only several meters from SinoChem Chongqing Fuling Chemicals Co's old industrial sewage drainage site.
Many local residents in Fuling, a mountainous county located at the banks of Wujiang River, can still recall the noxious "red dragon" and "white dragon" running side-by-side from a local fertilizer factory's drains into the upstream tributary of the Yangtze river.
The red and white dragons, were the residents' nicknames for two drainages that discharged thousands of tons of industrial waste from SinoChem Chongqing Fuling Chemicals Co located in southwest China's Chongqing municipality into the Wujiang River in the 1980s.
The "red dragon" contained ferric oxide, while the "white dragon" was MAP or monoammonium phosphate.
The fertilizer plants' toxic air and water emissions were a nightmare for the Fuling residents.
Zhao Liming, the director of Fuling county's environment protection bureau, who was born and grew up in the county, recalls that when he was a middle school student, at the chemistry class, his chemistry teacher told them, "If you want to figure out how sulfuric hydrogen smells, just go to the fertilizer chemical factory."
"The smell there was really bad and strong, like rotten eggs," Zhao recalls.
Last month, when a group of Chinese journalists came to visit the factory, an old man was spotted fishing at a site on the riverbank, only several meters away from the old drainage, which was dry.
The factory previously had seven waste drainages into the Wujiang River. But now they have been reduced to one, which is kept in case of emergency emissions.
At the only remaining drain, a 24-hour environmental monitor was installed to supervise the discharged water quality to make sure that the pollution index is at or below the national safety standard.
After the Three Gorges Dam was built, environmental protection for the Wujiang, the longest tributary on the southern bank of the Yangtze river, became a pressing issue for SinoChem Chongqing Fuling Chemicals Co, the offending fertilizer factory. In 2000 plant officials began working on cleaning up the pollution
By 2007, SinoChem Chongqing Fuling Chemicals Co finally achieved its goal of zero-emission of industrial sewage, and about 95.7 percent industrial water can now be recycled.
During the 10th Five-Year Plan period (2000-2005), the energy consumption for per unit of GDP and industrial added value respectively was reduced by 81.69 percent and 57.64 percent respectively. The ecompany saved 1.6 million tons of coal equivalent and 26.08 million tons of water, it reported.
The comprehensive energy consumption for producing per 10,000-yuan industrial output was reduced from 1,089 kg coals equivalent in 2004 to 532 kg coals equivalent in 2007, the company says.
SinoChem Chongqing Fuling Chemicals Co is a major subsidiary of Hong Kong-listed Sinofert Holdings Ltd, the only domestic fertilizer producer on the Hong Kong board.
As one of the nation's key fertilizer producers, it manufactures 30 types of fertilizer including calcium super phosphate, ammonium bicarbonate, and some high concentration fertilizers such as DAP, MAP and NPK as well as sulfuric acid and ammonia.
In 2007, SinoChem Chongqing Fuling Chemicals produced 1.5 million tons of fertilizer, 1.3 million tons of sulfuric acid and 60,000-tons of ammonia.
It posted 2.42 billion yuan industrial output and 2.25 billion yuan annual sales revenue last year, on which profits and taxes reached record high at 139 million yuan.
Water recycling system
For a chemical enterprise, water is a key and most-consumed resource.
"In the past, the company pumped one ton of water from Wujiang River, consumed 20-30 percent in the production lines, and the rest, 700-800 kg, flowed back into Wujiang River again. It not only wasted water resources but also polluted the river," says Sheng Yong, the company's chief engineer.
The company has since installed a more efficient water processing system that uses water more efficiently and can also extract phosphor and sulfur materials worth 5 million yuan every year, the company says.
"The waste we discharged into Yangzter River has now been turned into a valuable material and resource for our by-products manufacturing," says Wangchuan, general manager of SinoChem Chongqing Fuling Chemicals.
In the 1980s, the factory consumed 120 tons of water to produce one ton of sulfuric acid, and only 2.81 tons of water in 2007, the company says.
Moreover, in the early 1990s, the water consumption for producing a ton of ammonium bicarbonate was 40 tons, compared to 2.03 tons last year, the company says.
"The factory has expanded its production lines and enlarged capacity about tenfold since the factory was built. However, the source water pumping equipment is still the original equipment, yet the industrial water consumption has not increased sharply," says Wang Chuan.
Developing recycling business
Many companies may feel that pouring money into environmental protection is unprofitable, but as Wang points out SinoChem's investment has been paid back.
The company has made a big effort to develop its recycling business and changed the old business mode of "resource- product- waste-discharge" into the new recycling business mode "resource-product-renewed resources- byproducts".
Since 2004, the company has invested 80 million yuan in upgrading and introducing recycling and anti-pollution equipment.
The huge amount of gypsum residue waste generated by phosphorous ammonia fertilizer manufacturing also used to be a big headache for Sinochem.
In 2006, the company invested 30 million yuan to build a cement plant with an annual capacity of 200,000 tons and a gypsum plant with 100,000 tons of annual capacity.
Thanks to these two plants, the gypsum residue waste is used to make cement and land plaster, a new construction material, using 400,000 tons of phosphorus gypsum every year. The residue generated in manufacturing sulfuric acid with sulfuric iron ore was also used as an additive in cement production.
Sulfuric acid production also generates a large amount of heat energy. To make better use of it, the company has installed a system that can use the waste heat to generate electricity and supply heating for the factory buildings. Last year, the waste heat electricity system generated 60 million kW/h of electricity, saving 18 million yuan in energy costs.
(China Daily June 2, 2008)